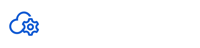
Secure remote access for industrial machines
Stay connected to your machines no matter where you are. IXON’s cloud-based remote access provides a secure, high-performance solution to streamline maintenance, reduce downtime and enhance efficiency.
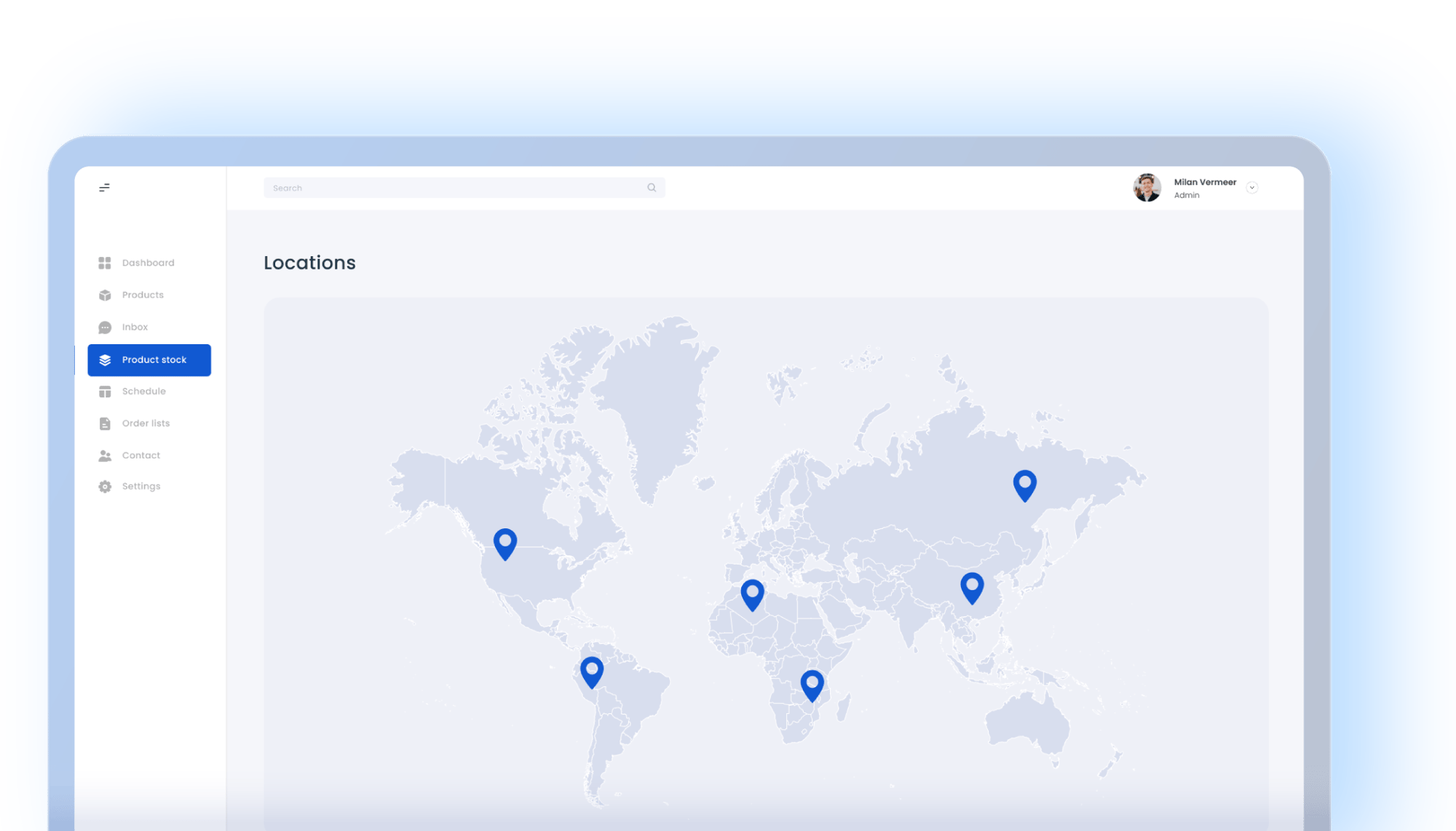
Why choose IXON for remote access?
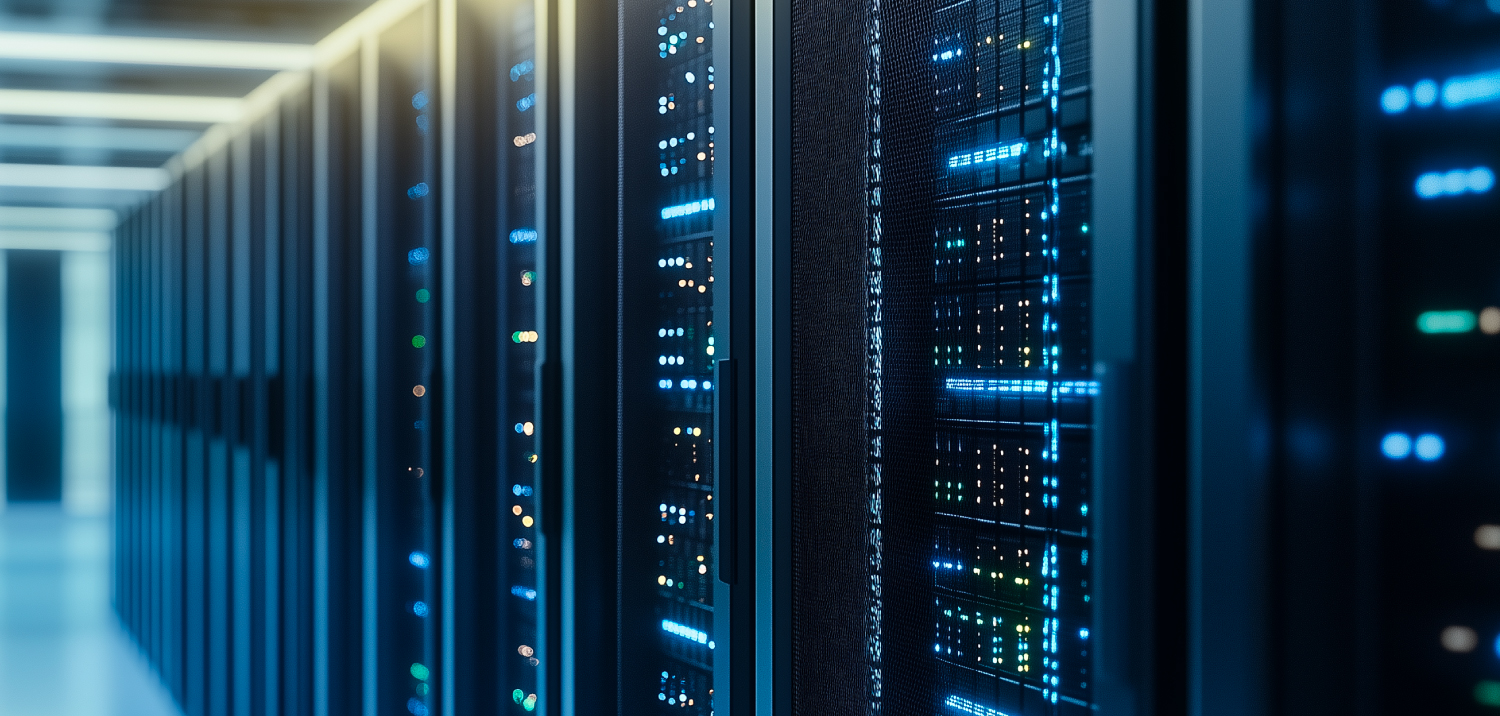
Secure & reliable connectivity
IXON ensures a secure connection including a built-in firewall, VPN encryption and role-based access control to prevent unauthorized access. We are certified to multiple ISO standards and IEC 62443 to protect you from cyber threats.
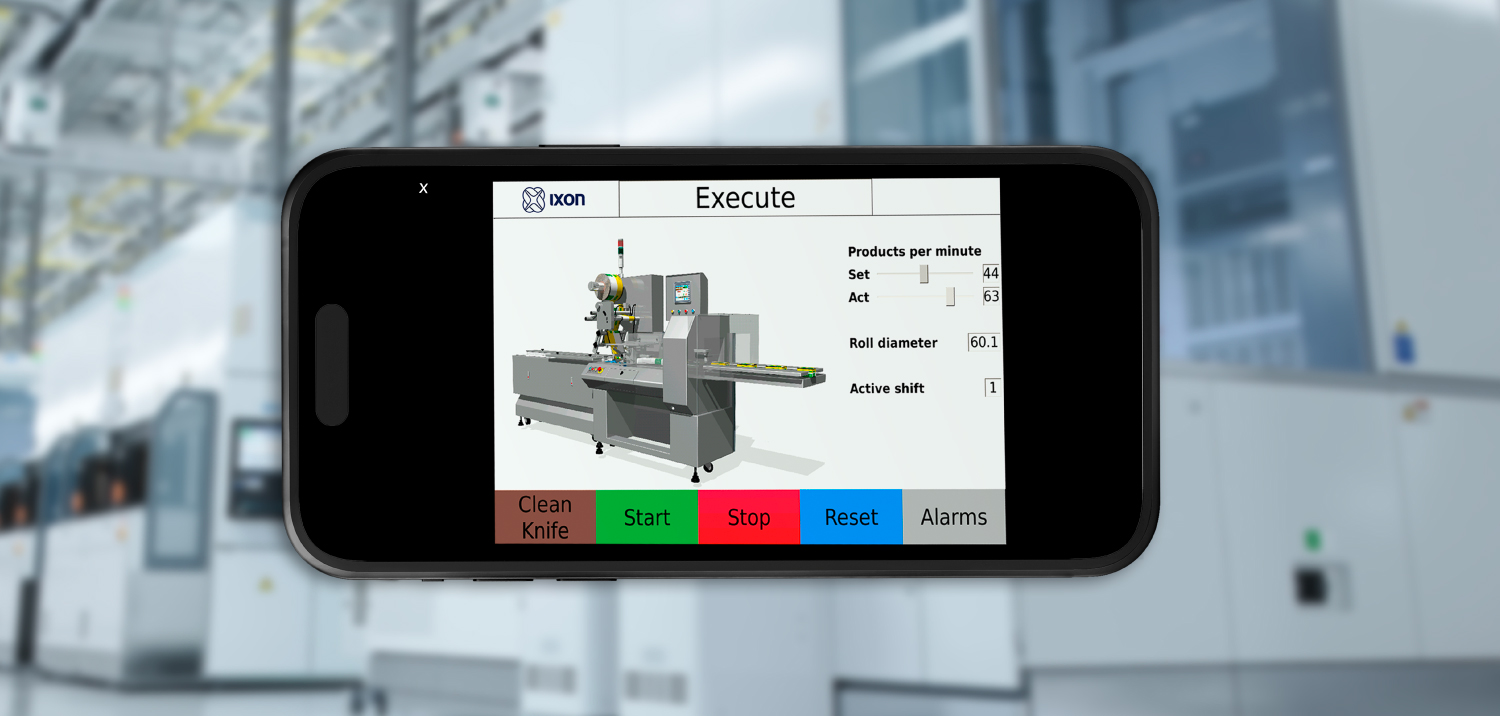
EasyControl for your machine
With just one click in IXON Cloud or the IXON app, you and your customers can access the touch panel of your machine remotely, even without technical knowledge. EasyControl is available for touch panels with VNC or HTTP.

Licence-free & easy collaboration
Remote Access Cloud allows for license-free access, enabling seamless and secure collaboration with colleagues, customers and partners without extra costs or security compromises.
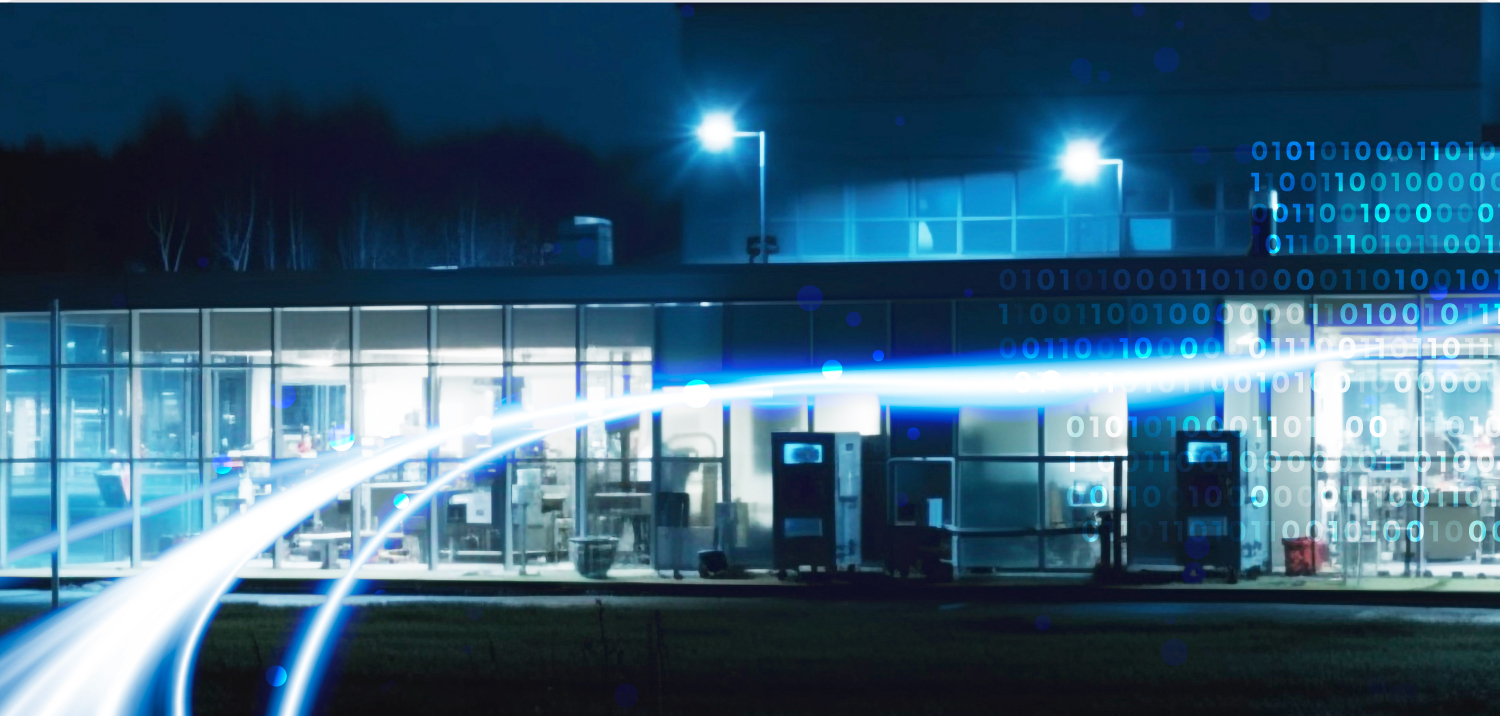
High-speed & web-based
Users can establish a stable, high-speed VPN connection to e.g. PLCs and HMIs from any browser. Web-based access makes local VPN clients unnecessary, making it more efficient.
Features
DirectVPN
Direct VPN access to machine controllers via the cloud to work remotely with your engineering tools.
EasyControl (VNC and HTTP)
One-touch access to the control or web panel of your machine from the browser and from the IXON app.
Concurrent connections
The IXON licensing structure has no restrictions on the number of users allowed to simultaneously connect to a remote machine via DirectVPN or EasyControl.
Advanced user & device management
Roles, groups and access profiles allow extensive selection of who gets access to which functionality. Be it internal employees, distributors or customers.
Read more about user management
Data logging to MQTT broker
IXON edge gateways have the ability to send data via MQTT to 3rd party cloud providers. Configuration can easily be done via IXON Cloud.
Read more about MQTT
Remote firmware upgrades
A listing of current firmware versions with release notes is available. These can be easily installed on remote IXON edge gateways.
Check our release notes here.
Access request and approval
Empower your customers with full control over remote access to their machines. The Request Access feature ensures secure, transparent collaboration by requiring machine builders to request permission before connecting.
- Easy one-click approval or denial via email
- Complete visibility with access requests and sessions logged in the customer portal
- Aligns with NIS security guidelines
Service Logbook
Keep track of all service activities in one central place with the Service Logbook. Record important details such as configuration changes, maintenance tasks and any issues encountered.
With a shared overview of service history, your team stays informed, aligned and ready to act.
Read more about the Service Logbook here.
LAN Access Management
Give certain users only DirectVPN access to one part of the network within the machine.
Connection monitoring and alerting
The connections of your edge gateways are monitored. When a connection is not active for X period of time, a notification can be sent to selected users.
Temporary access
Give a user only access for a short period of time. This ensures that you never forget to revoke someone's access manually.
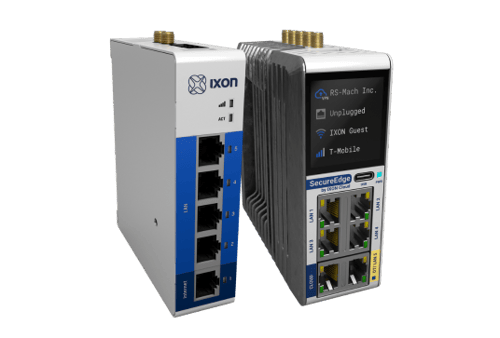
Edge gateways that are easy to set up
The no-code, plug-and-play installation ensures a quick, hassle-free setup
that’s accessible to both technical and non-technical users.
What our customers say
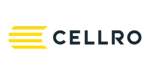
“We can solve 90% of issues remotely. The remaining 10% that needs to be solved at the customer’s location can be solved more targeted.”
Michel van Kleinwee
Service & Software Engineer at Cellro
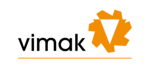
"Thanks to IXON we intervene remotely as if we were in front of the machine, allowing us to solve software-related issues and prepare for on-site trips in advance.''
Riccardo Erasti
Sales Director at Vimak
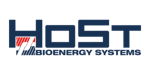
“I dare to say that IXON is the most important remote service component with us. The speed of troubleshooting has increased tenfold.”
Vincent Kroeze
Process Engineer Service at Bright Services
Discover how easy & secure remote access can be
Learn more about the benefits of Remote Access Cloud and how our solution is designed with security as a top priority. We'll help you communicate a strong security story to your customers so you can enter the conversation with confidence.
Frequently asked questions
What is (industrial) remote access?
Industrial remote access refers to the ability to remotely connect to and control industrial machines, such as PLCs (Programmable Logic Controllers) and HMIs (Human-Machine Interfaces), over the internet. This is typically achieved using secure VPN connections, allowing technicians to perform tasks such as monitoring, troubleshooting, and configuring equipment from anywhere, at any time.
What is a remote connection?
A remote connection is a link established over the internet that allows a user to access and control a device or system from a different physical location. In an industrial context, this often involves connecting to machines or control systems to perform maintenance, updates, or diagnostics remotely.
How does remote access for machines work?
Remote access works by using devices like the IXrouter, which creates a secure connection between the industrial machine and the cloud platform. The connection is typically established via a VPN, ensuring data is encrypted and secure. Once connected, users can access the machine’s control panels and view diagnostic information.
Here’s how it works with IXON Cloud:
- Connection setup
A device like the IXrouter is installed on the machine site. This device connects to the internet via Ethernet, Wi-Fi, or 4G. - Secure VPN tunnel
The IXrouter establishes a secure VPN tunnel to the IXON Cloud, ensuring all data transmitted is encrypted and secure. - Access and control
Authorized users can then remotely access the machine via the IXON Cloud using various services such as VNC (for remote desktop access), HTTP (for web interface access), and WebSocket. This setup allows users to monitor, troubleshoot and update machines from any location.
What are the advantages of remote access for machine builders?
The benefits of remote access for machine builders include:
- Reduced downtime: Quickly address issues without waiting for on-site visits.
- Cost savings: Lower travel and labor costs by reducing the need for physical presence.
- Increased efficiency: Perform updates and maintenance tasks more efficiently.
- Enhanced support: Provide better support to customers and operators by accessing machines remotely.
- Scalability: Easily manage multiple machines and locations from a central point.
Application of remote access in the industry
Remote access is widely used for:
- Remote troubleshooting and maintenance of machinery.
- Remote programming and configuration of PLCs.
- Monitoring and data logging from industrial devices.
- Providing support and training to on-site staff.
- Commissioning new equipment and systems remotely.
What are the use cases for remote access?
- Remote troubleshooting: Diagnosing and fixing issues without the need for on-site visits.
- Preventive maintenance: Monitoring equipment to predict and prevent failures.
- Remote monitoring: Continuously observing machine performance and conditions.
- Configuration and updates: Remotely updating software or configurations on industrial devices.
- Support and training: Providing real-time support and training to on-site operators.
Read here how IXON customers use remote access.
Is remote access absolutely secure?
While no system can be guaranteed to be 100% secure, IXON implements multiple security measures to ensure high levels of protection. This includes using VPNs for encrypted connections, built-in firewalls in their edge gateways to separate networks, role-based access control (RBAC), and compliance with international security standards such as ISO 27001, ISO 27017, ISO 27701 and IEC 62443.
How is the security of remote access guaranteed?
The security of remote access is guaranteed through multiple layers of protection:
- Encrypted VPN tunnels: All data transmissions between the machine and the cloud are encrypted using secure VPN tunnels, preventing unauthorized access.
- Built-in firewalls: IXON’s edge gateways have a built-in firewall that separates the machine network from the factory's internal network, adding an extra layer of protection.
- Role-based access control (RBAC): Access to machines and data is managed through RBAC, ensuring that only authorized users can access specific functions and data.
- Two-factor authentication (2FA): Additional security is provided by requiring 2FA for user access, significantly reducing the risk of unauthorized access.
- Compliance with security standards: IXON adheres to international security standards such as ISO 27001, ISO 27017, ISO 27701 and IEC 62443, ensuring a high level of security and regular audits to maintain compliance.
Can industrial remote access be integrated into existing systems?
Yes, industrial remote access can be integrated into existing systems. IXON provides open APIs that allow for seamless integration with various IT and OT systems. This integration enables:
- Data exchange: Secure data exchange between machines and enterprise systems like ERP, CRM, and other business applications.
- Automation: Automated configuration workflows for deploying new equipment and pushing updates directly from existing systems.
- Custom solutions: Development of custom applications and services tailored to specific business needs, enhancing the overall IIoT infrastructure.
- Scalability and flexibility: The open and documented APIs ensure that the solution is future-proof and can adapt to evolving business requirements without vendor lock-in.
Read more about integrations here or take a look at our Marketplace.