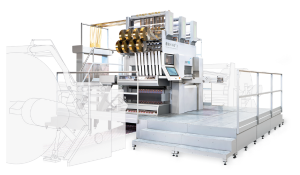
- Home
- IIoT Plattform
- Maschinenleistung analysieren
Maschinendatenerfassung: Einfach zu bedienendes Datenüberwachungs- und Analysetool für Industriemaschinen
Viele Maschinenbauer lassen sich von der Komplexität der Datenanalyse und der Maschinendatenerfassung einschüchtern. IXON Cloud macht es einfach, Einblicke in den Echtzeitstatus Ihrer Maschine zu erhalten oder historische Daten auf Performance-Trends zu überwachen. So können Sie Ihre Maschinen kinderleicht optimieren.
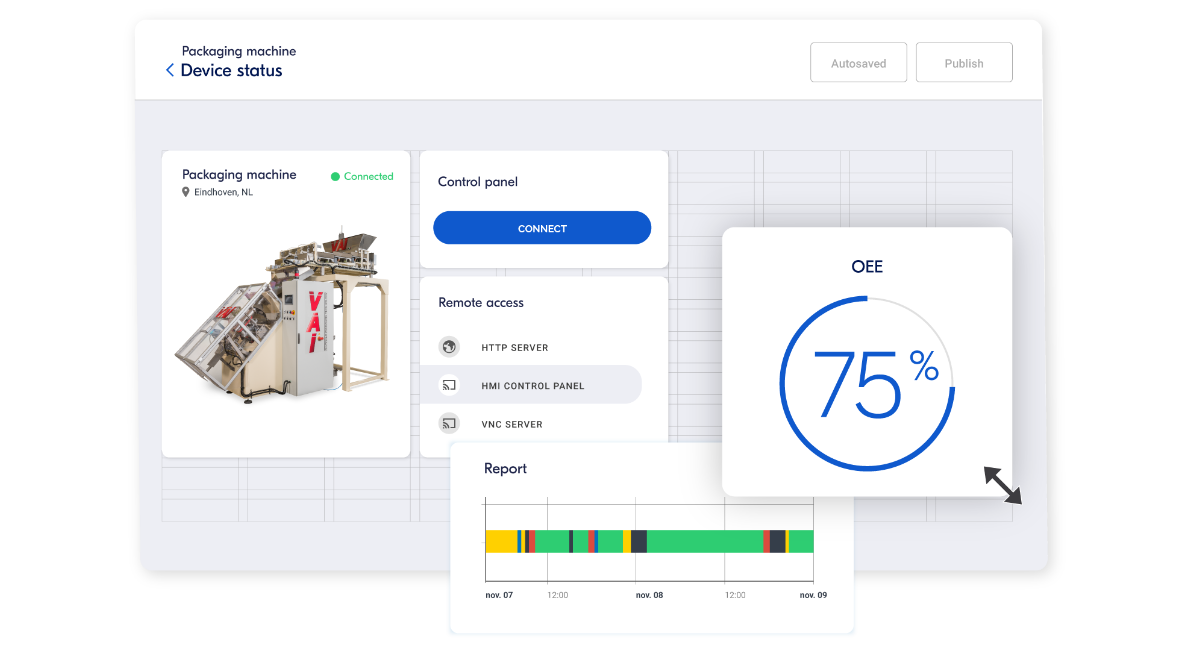
Optimieren Sie die Maschinenleistung durch Maschinendatenerfassung und Dateneinblicke
Zustandsüberwachung in Echtzeit
In individuell anpassbaren Daten-Dashboards behalten Sie bestimmte Datenparameter im Auge, die auf eine Verschlechterung der Maschinenleistung oder einen drohenden Ausfall hinweisen.
Maschinenausfall vorhersagen
Entdecken Sie Muster in Ihren Maschinendaten. Beginnen Sie mit der Vorhersage des Wartungszeitpunkts, damit Sie Ausfällen vorbeugen und ungeplante Ausfallzeiten vermeiden können.
Datengestützte Optimierung der Anlagen
Optimieren Sie Komponenten, die nicht den Anforderungen entsprechen, und erhalten Sie so optimal laufende Maschinen, die nie stillstehen.
Hochflexible Lösung für die Analyse der Maschinenleistung
Echtzeit- und historische Daten
Erfassen und visualisieren Sie Daten von Ihren SPS, Sensoren oder Robotern in Echtzeit oder in historischen Dashboards. Überwachen Sie den Maschinenzustand, um Probleme zu diagnostizieren und Fehler aus der Ferne zu beheben.
Zuverlässige Datenspeicherung
IXON Cloud ist von Haus aus sicher, d. h. die Sicherheit ist in die Infrastruktur und die grundlegenden Prozesse integriert. Wir gewährleisten eine schnelle und genaue Datenspeicherung und die volle Verfügbarkeit Ihrer Daten zu jeder Zeit.
Weitreichend kompatibel
Die IXON-Lösung ist offen kompatibel mit allen Industriestandards. Zu den unterstützten Kommunikationsprotokollen gehören Modbus, OPC UA und Ethernet/IP. Eine vollständige Liste finden Sie hier.
Offenes Betriebssystem
Um eine Herstellerbindung zu vermeiden, ist das IXON Cloud-Ecosystem offen für die Integration und Verknüpfung mit über 1000 Tools und Systemen über die IXON API. Es steht Ihnen frei, Ihre Daten in jedes beliebige Tool oder System zu exportieren.
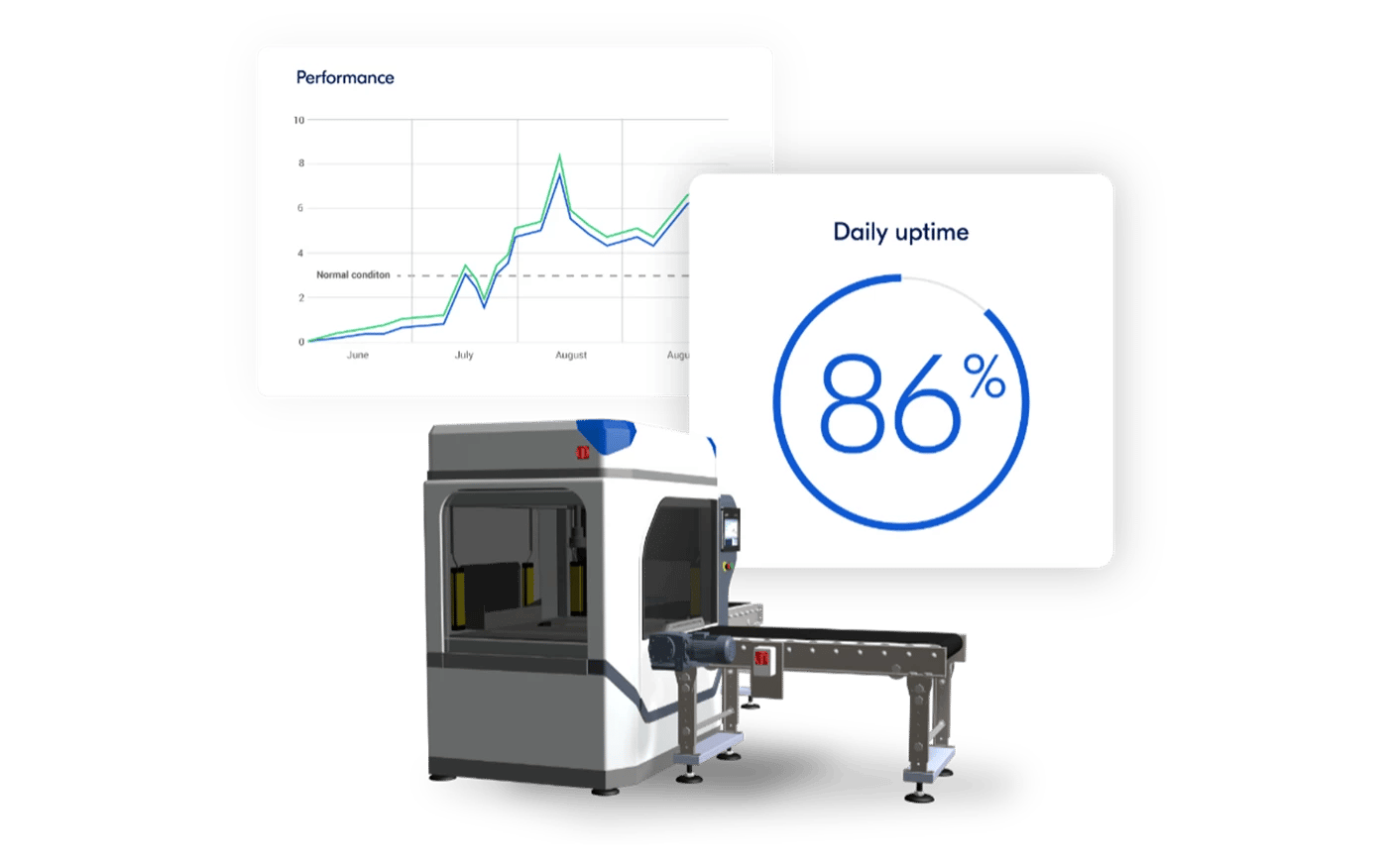
Create KPI-driven dashboards
Erstellen Sie Ihre eigenen erweiterten Maschinen-Dashboards mit wichtigen Datenanalysepunkten, um Fehler auf einen Blick zu erkennen. Verwenden Sie Ihre Dashboards für verschiedene Zwecke, z. B. für die Überwachung des Maschinenzustands, um Trends in Ihren Maschinendaten zu erkennen oder um Ausfälle vorherzusagen, bevor sie auftreten. Gewähren Sie Ihren Kunden Einblick in ihre Maschinendaten, indem Sie ihnen Zugang zum Portal gewähren, und geben Sie KPI-Dashboards für Maschinen einfach weiter. Lassen Sie Komponenten anzeigen mit:
- Kritischen Maschinenparametern, z. B. Vibration, Druck oder Temperatur
- Produktionsdaten wie Anzahl der produzierten Einheiten, Menge an Verschnitt oder Abfall
- Gesamtanlageneffektivität (OEE)
Andere wichtige - Maschineninformationen wie Maschinenhandbücher
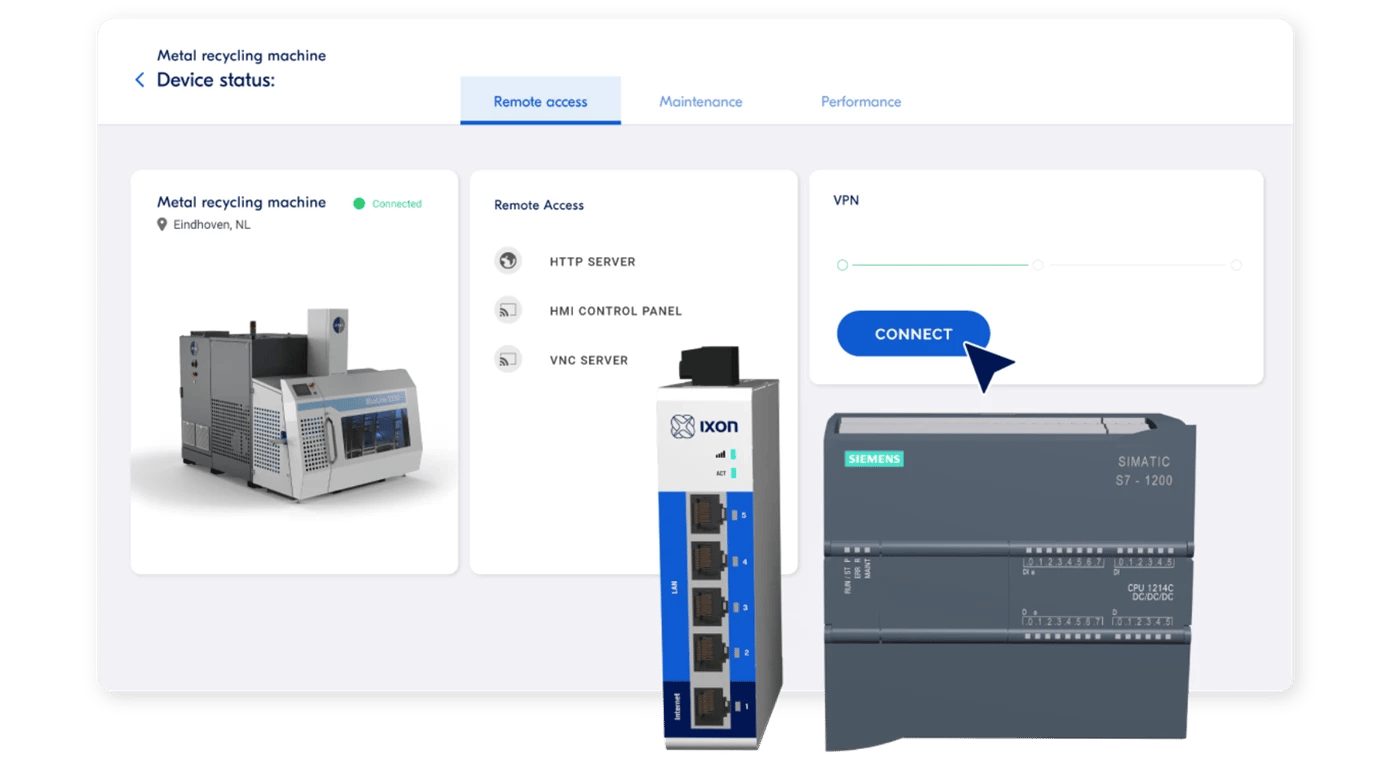
One-Stop-Shop für den Maschinenzugang
Die IXON Cloud-Plattform ist eine All-in-One-IIoT-Lösung mit einem breiten Spektrum an Funktionen. Alles, was Sie brauchen, um die Produktivität Ihrer Maschinen an einem Ort zu maximieren: vom einfachen industriellen Fernzugriff bis hin zur erweiterten Datenprotokollierung, Maschinenalarmen und benutzerdefinierten Dashboards.
Alle wichtigen Informationen über Ihre Maschinen werden auf einer zentralen Plattform gesammelt und einer Vielzahl von Benutzern zur Verfügung gestellt. Bieten Sie Ihren Kunden, Serviceteams, Softwareingenieuren oder Mechanikern einen sicheren Zugang mit individuellen Ansichten. Die Benutzerfreundlichkeit von IXON Cloud macht Ihr Service-Portal für jeden funktional.
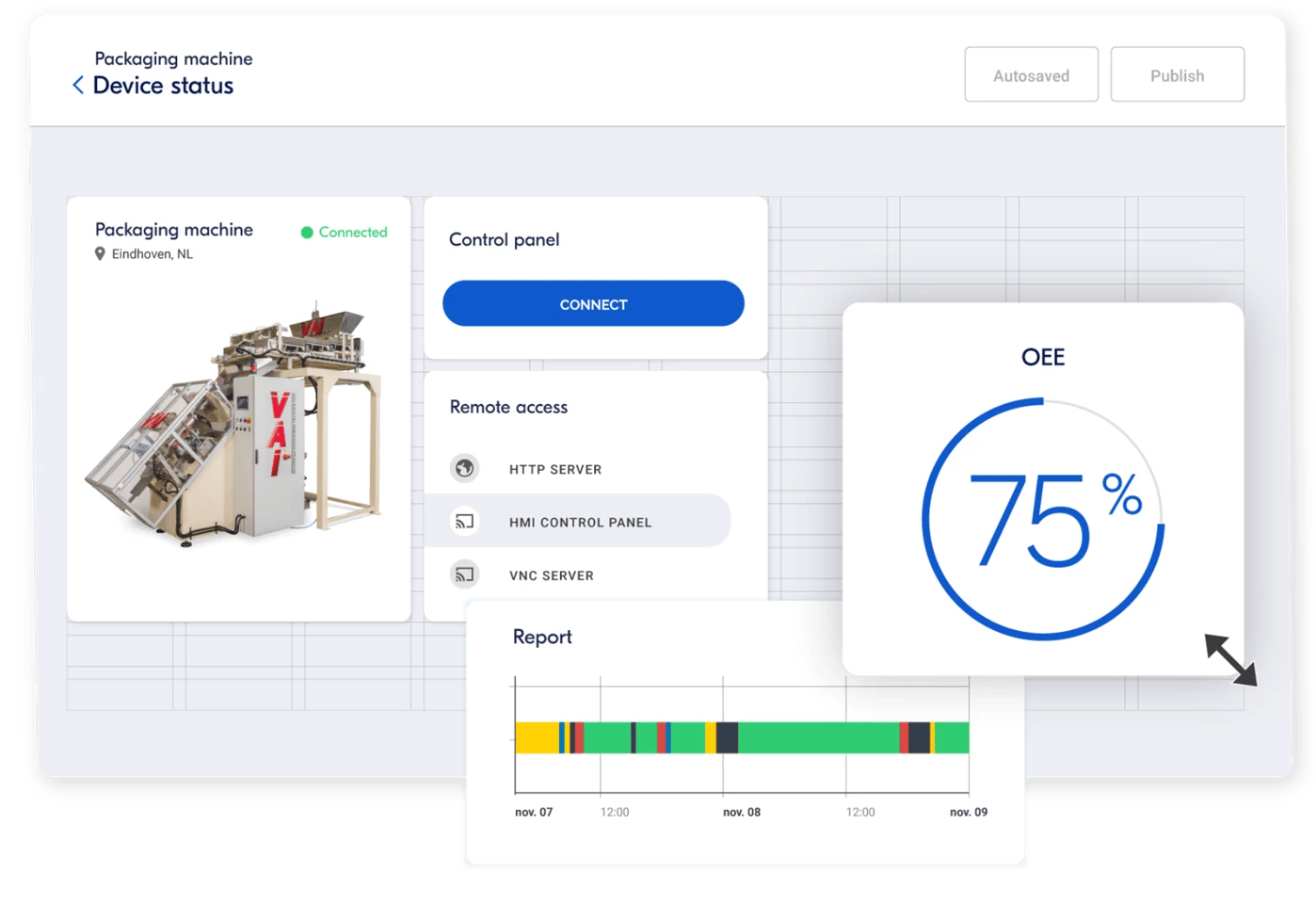
Vollkommen anpassbar an Ihre Bedürfnisse
Die Anpassungsfähigkeit von IXON Cloud erstreckt sich auch auf die Daten-Dashboards. Per Drag & Drop können Sie Ihre Maschinen-Dashboards ganz einfach an Ihre Anforderungen anpassen. Sie können die von Ihnen gewählten Komponenten so anordnen, wie es für Sie am besten passt, und individuelle Dashboards oder pdf-Berichte für verschiedene Benutzertypen erstellen. Auf diese Weise sieht jeder nur die Daten, die seinen persönlichen Interessensschwerpunkten entsprechen.
Falls die vorkonfigurierten Optionen Ihren Anforderungen nicht genügen sollten, können Sie mit der Component SDK auch Komponenten für benutzerdefinierte Datendiagramme erstellen oder Daten aus externen Ressourcen integrieren.
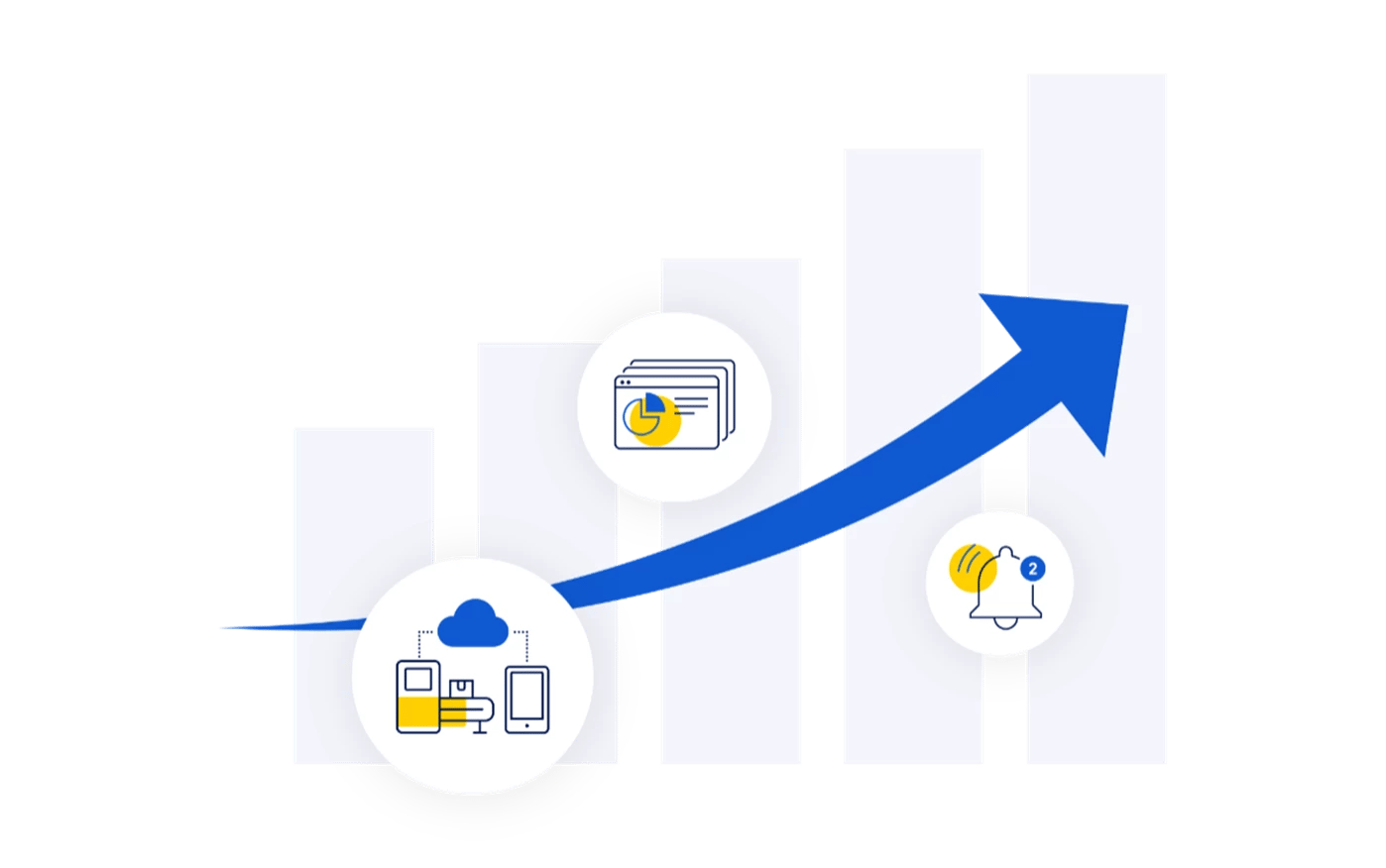
Zukunftssicher & skalierbar
IXON Cloud ist für jeden geeignet, der sich mit Maschinendatenerfassung befasst. Vom KMU, das heute nur ein einfaches Dashboard benötigt oder weiß, dass es in naher Zukunft auf fortschrittlichere Technologien umsteigen möchte, bis hin zu großen multinationalen Unternehmen, die sofort kombinierte Dateneinblicke von mehreren Maschinen benötigen. Eine sofort einsatzbereite Plattform mit allen Tools, die für eine erfolgreiche Zukunft erforderlich sind.
- Beginnen Sie noch heute mit der einfachen, standardmäßigen Einrichtung der Plattform
- Erweitern Sie sie mit Anpassungen, wenn Sie bereit sind, sie zu erweitern
- Erweiterte Integrationen mit der IXON API möglich
- Erschließen Sie neue Geschäftsmodelle wie Lifecycle Management
FAQ´s
Was ist Maschinendatenerfassung?
Bei der Maschinendatenerfassung (MDE) geht es um die Erfassung und Speicherung von Daten, die von industriellen Maschinen und Geräten wie speicherprogrammierbaren Steuerungen (SPS), Mensch-Maschine-Schnittstellen (MMS), Sensoren und anderen Geräten erzeugt werden. Diese Daten werden zur weiteren Analyse und Optimierung industrieller Prozesse verwendet. IXON verwendet Geräte wie den IXrouter und das SecureEdge Pro Gateway, um Daten von verschiedenen Parametern zu sammeln, zu speichern und zur Verarbeitung und Analyse an die IXON Cloud zu senden.
Warum Maschinendatenerfassung verwenden?
Maschinendatenerfassung (MDE) wird eingesetzt, um Informationen über die Leistung und den Zustand von Industrieanlagen zu erhalten. Durch die Erfassung von Maschinendaten können Unternehmen wichtige Leistungsindikatoren (Key Performance Indicators, KPIs) überwachen, die Maschineneffizienz verfolgen und Bereiche mit Verbesserungspotenzial identifizieren. Dies führt zu einer besseren Entscheidungsfindung, einer höheren Betriebseffizienz und der Möglichkeit, Maschinenausfälle vorherzusagen und zu verhindern.
Welche Rolle spielt Maschinendatenerfassung bei der Ausfallzeitprävention?
Die Maschinendatenerfassung spielt eine entscheidende Rolle bei der Vermeidung von Ausfallzeiten, da sie eine Echtzeitüberwachung und zustandsorientierte Wartung ermöglicht. Durch die kontinuierliche Erfassung und Analyse von Daten können Unternehmen Anomalien und Anzeichen für potenzielle Ausfälle frühzeitig erkennen. Auf diese Weise können Wartungsteams Probleme beheben, bevor sie zu ungeplanten Ausfallzeiten führen.
Wie hilft Maschinendatenerfassung bei der Fehlerprognose?
Durch die Überwachung von Parametern wie Temperatur, Vibration und Druck können Unternehmen Muster und Trends erkennen, die auf einen bevorstehenden Ausfall hindeuten. Dieser proaktive Ansatz ermöglicht eine rechtzeitige Wartung und Reparatur und verringert die Wahrscheinlichkeit unerwarteter Maschinenausfälle.
Welche Vorteile bietet die Integration von Maschinendatenerfassung in IoT-Systeme?
- Echtzeit-Überwachung: Ermöglicht die kontinuierliche Überwachung der Maschinenleistung und des Maschinenzustands von jedem Standort aus.
- Verbesserte Wartung: Erleichtert die vorausschauende und vorbeugende Wartung und reduziert Ausfallzeiten und Wartungskosten.
- Datengetriebener Einblick: Liefert wertvolle Daten für die Analyse und hilft, den Betrieb zu optimieren und die Effizienz zu verbessern.
- Fernzugriff: Ermöglicht Fehlerbehebung und Support aus der Ferne und reduziert so die Notwendigkeit von Besuchen vor Ort.
- Skalierbarkeit: Unterstützt die Integration mehrerer Geräte und Systeme und erleichtert so die Verwaltung komplexer industrieller Prozesse.
Kundengeschichten zur Maschinendatenerfassung und Analyse der Maschinenleistung
IXON Preise
Entdecken Sie die am besten geeigneten Produkte und Pläne für Ihren Bedarf.
Persönliche Demo anfordern
Entdecken Sie in einem 1:1-Gespräch, was IXON für Sie tun kann.